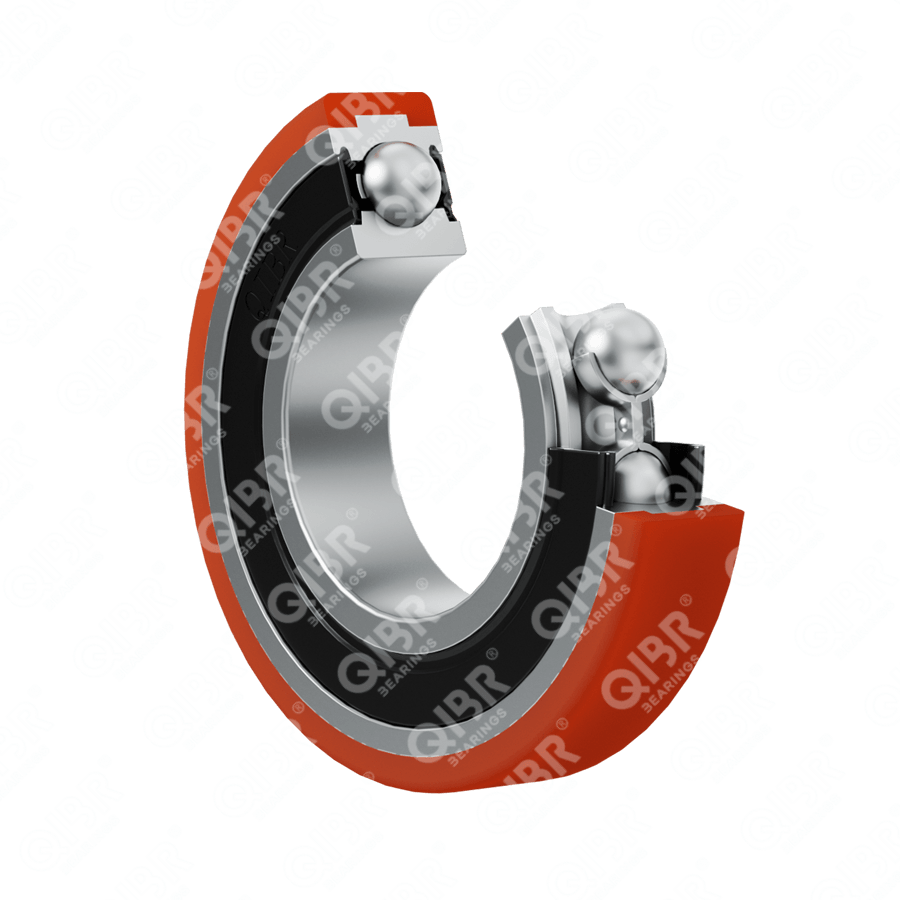
Изображения могут отличаться от продукта. Подробнее см. технические характеристики.
Поиск нужной модель подшипника.
Стандарт
GB,ASTM/AISI,ГОСТ,BS,JIS,NF,DIN/VDEh,DIN/VDEh
Внутренний диаметр
5mm-8mm
Наружный диаметр
22mm-45mm
Ширина
9mm-15mm
Базовая динамическая нагрузка, радиальная
45lbf-85lbf
Материал покрытия
NDI/POM Polyurethane
Номинальная статическая нагрузка, радиальная
16lbf-33lbf
Макс. частота вращения
19.2-21.6(X1000 rpm)
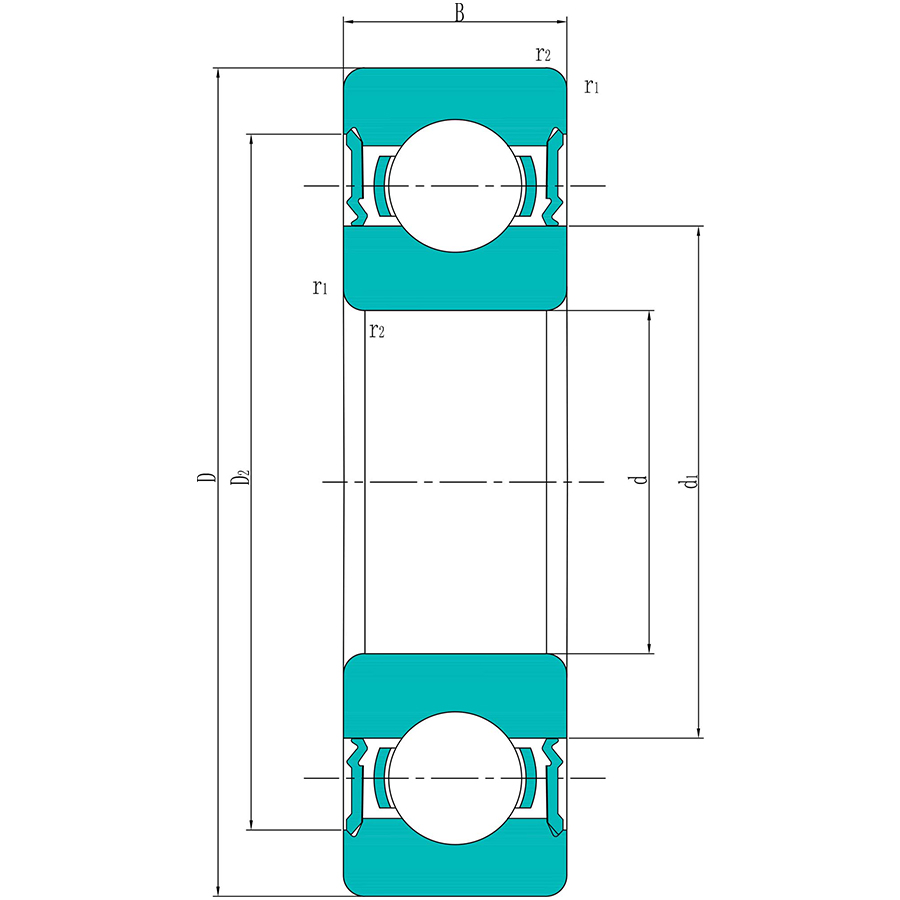
NO. | Product | Product Number | Отверстие | Тип внутреннего кольца | Наружный диаметр (D) | Тип уплотнения | Материал щита | Ширина внутреннего кольца |
---|---|---|---|---|---|---|---|---|
1 |
![]() |
625 2rs | 5 mm | Extended | 22 mm | Sealed | NBR | 12 mm |
2 |
![]() |
625 2rs | 5 mm | Extended | 25 mm | Sealed | NBR | 12 mm |
3 |
![]() |
626 2rs | 6 mm | Extended | 30 mm | Sealed | NBR | 12 mm |
4 |
![]() |
626 2rs | 6 mm | Extended | 30 mm | Sealed | NBR | 16 mm |
5 |
![]() |
626 2rs | 6 mm | Extended | 30 mm | Sealed | NBR | 16 mm |
6 |
![]() |
626 2rs | 6 mm | Extended | 30 mm | Sealed | NBR | 16 mm |
7 |
![]() |
626 2rs | 6 mm | Extended | 35 mm | Sealed | NBR | 16 mm |
8 |
![]() |
608 2rs | 8 mm | Extended | 35 mm | Sealed | NBR | 18 mm |
9 |
![]() |
608 2rs | 8 mm | Extended | 40 mm | Sealed | NBR | 13 mm |
10 |
![]() |
608 2rs | 8 mm | Extended | 40 mm | Sealed | NBR | 15 mm |
11 |
![]() |
608 2rs | 8 mm | Extended | 40 mm | Sealed | NBR | 15 mm |
12 |
![]() |
608 2rs | 8 mm | Extended | 40 mm | Sealed | NBR | 18 mm |
13 |
![]() |
608 2rs | 8 mm | Extended | 45 mm | Sealed | NBR | 16 mm |
14 |
![]() |
608 2rs | 8 mm | Extended | 45 mm | Sealed | NBR | 18 mm |
Особенности и преимущества полиуретанового махового колеса QIBR
Полиуретановое маховое колесо IBR решает несколько важнейших проблем в различных областях, в основном в следующих областях:
1. Выступающая конструкция внутреннего кольца
Выступающая часть внутреннего кольца полиуретанового махового колеса QIBR помогает повысить грузоподъемность и стабильность подшипника, особенно в приложениях с высокими требованиями к нагрузке. Она может улучшить механические характеристики за счет увеличения площади контакта подшипника.
2. Поглощение ударов и снижение шума
Полиуретановое маховое колесо QIBR обладает хорошей эластичностью и буферными свойствами, эффективно поглощая вибрации и снижая шум.
3. Устойчивость к воздействию масла и химической коррозии
Полиуретановое маховое колесо QIBR обладает хорошей устойчивостью к маслам, растворителям и различным химическим веществам.
4. Ударопрочность
Высокая эластичность полиуретанового махового колеса QIBR обеспечивает хорошую ударопрочность, что делает его подходящим для сред с ударными нагрузками.
Улучшение характеристик и решения для полиуретанового махового колеса QIBR
1. Повышение износостойкости
Добавление армирующих материалов (например, сажи, керамики, металлических порошков) позволяет повысить твердость и износостойкость полиуретана, обеспечивая стабильную работу при повышенных нагрузках и длительных условиях эксплуатации.
2. Повышение масло- и химической стойкости
В зависимости от условий применения выбор полиуретановых составов с повышенной стойкостью к химическим веществам и маслам может продлить срок службы подшипников в сложных условиях.
3. Оптимизация толщины полиуретанового слоя
Толщина полиуретанового слоя напрямую влияет на рабочие характеристики подшипников. Соответствующая толщина может повысить ударопрочность и износостойкость. Однако чрезмерная толщина может снизить жесткость подшипников, что негативно скажется на их эксплуатационных характеристиках. Хорошо спроектированный полиуретановый слой обеспечивает баланс между амортизацией, износостойкостью, несущей способностью и эксплуатационной стабильностью.
4. Оптимизация структуры внутренних и наружных дорожек качения
Оптимизация геометрии и размеров внутренних и наружных дорожек качения позволяет равномерно распределить усилие на полиуретановый слой, избегая локального чрезмерного износа.
Основные области применения полиуретанового махового колеса QIBR
1. Автомобильная промышленность
Полиуретановые подшипники широко используются в автомобильном секторе, особенно в системах подвески, привода и тормозных системах. Благодаря поглощению вибраций, снижению шума и долговечности они используются в:
автомобильных колесных осях и системах подвески;
компонентах двигателей и трансмиссий;
колесах и тормозных системах.
2. Машиностроение
В машиностроении полиуретановые подшипники используются в различных высоконагруженных и износостойких механизмах. Их эластичность и прочность позволяют им работать в условиях больших нагрузок и сильных ударов.
3. Спортивное оборудование
Полиуретановые подшипники часто встречаются в спортивном оборудовании и инструментах, требующих износостойкости и ударопрочности, в том числе:
Скейтборды;
Сноуборды;
Велосипедные коньки и другие спортивные снаряды.
4. Аэрокосмическая промышленность
В аэрокосмической отрасли полиуретановые подшипники предпочитают за их превосходную высокотемпературную и износостойкую прочность. Они часто используются в компонентах самолетов, которые выдерживают высокоскоростные операции и экстремальные условия окружающей среды.
5. Морская и оффшорная техника
Полиуретановые подшипники широко используются в морской и оффшорной технике, особенно в механических компонентах, которые часто подвергаются воздействию морской воды, соляного тумана и других агрессивных сред. Они обеспечивают превосходную коррозионную стойкость и долговечность.